How to repair the overflow foot edge of molded rubber products?
Release time:
2018-07-11
Edge trimming is a common process in the production of rubber products. The trimming methods are: manual trimming method, grinding method, cutting method, frozen trimming method, no flash mold molding method, etc. Each manufacturer can choose the appropriate trimming method according to the quality requirements of the product and its own production conditions. 1. The flash-free mold is produced by using the flash-free mold, and the trimming work becomes simple and easy (the flash will fall off as soon as it is torn, so this mold is also called the tear-off mold). No flash mold molding method, can completely omit the trimming process, improve product quality and performance, reduce labor intensity and production costs and other characteristics, has broad prospects for development. 2, cold.
Edge trimming is a common process in the production of rubber products. The trimming methods are: manual trimming method, grinding method, cutting method, frozen trimming method, no flash mold molding method, etc. Each manufacturer can choose the appropriate trimming method according to the quality requirements of the product and its own production conditions.
1. Mold without flash
The use of flash-free mold for production, trimming work becomes simple and easy (flash is torn off, so this mold is also called tear mold). No flash mold molding method, can completely omit the trimming process, improve product quality and performance, reduce labor intensity and production costs and other characteristics, has broad prospects for development.
2. Frozen trimming
The principle is to use liquid nitrogen (LN2) to make the raw edge of the finished product brittle at low temperature, and to use specific frozen particles (projectiles) to hit the raw edge to quickly remove the raw edge. The production efficiency of frozen trimming is high, the labor intensity is small, the trimming quality is good and the degree of automation is high, the trimming equipment is especially suitable for pure rubber parts. Applicable products widely, has become the mainstream of the process standard. However, this type of equipment is expensive and the operating cost is high.
3. Manual trimming
Manual trimming is an ancient trimming method, which includes punching the rubber edge by hand with a punch. Remove the rubber edge with scissors, scraping and other knives. The quality and speed of manually trimmed rubber products will also vary from person to person. It is required that the geometric dimensions of the trimmed products must meet the requirements of the product drawings, and there must be no scratches, scratches and deformation. Before trimming, the trimming parts and technical requirements must be clearly understood, and the correct trimming methods and tools must be mastered.
In the production of rubber miscellaneous parts, most of the trimming operations are manual operations in different forms. Due to the inefficient production of manual trimming, many people are often mobilized to trim when production tasks are concentrated. In this way, not only the work order is affected, but also the quality of the products is not guaranteed. To this end, consideration should be given to the use of more effective process measures (such as the use of flash-free forming mold) or the use of a variety of trimming equipment for trimming.
4. Mechanical trimming
There are mainly punching, grinding wheel edging and round knife trimming, suitable for specific products with low precision requirements. It is currently the leading approach to trimming.
① Low-temperature shot blasting trimming Precision products with high trimming quality requirements, such as O-rings, small leather bowls, etc., can be trimmed by this method. The product is quickly cooled to below the brittle temperature with liquid nitrogen or dry ice, and then the flash is broken and dropped by high-speed spraying of metal projectiles or plastic projectiles, and the end is trimmed.
Low temperature brush grinding trimming it is by means of two nylon brushes rotating around the horizontal axis to remove the rubber edge brush of frozen rubber products.
③ Low-temperature drum trimming is the earliest selected frozen trimming method. The impact force generated by drum transformation and the friction force between products are used to crack and fall off the flash of products frozen below the embrittlement temperature. The shape of the drum is usually octagonal to increase the impact force of products in the drum. The rotating speed of the drum should be moderate, and the power can be improved by adding abrasive. For example, the trimming technology of the rubber plug of the electrolytic capacitor is to choose the low-temperature drum trimming.
④ Low-temperature oscillation trimming is also called oscillation freezing trimming. The products do spiral oscillation in the circular sealing box, and there is a strong impact effect between the products and between the products and the abrasive, resulting in the frozen embrittlement of the rubber edge. The low temperature oscillation trimming is better than the low temperature drum trimming, the product damage rate is low, and the output power is higher.
⑤ Low-temperature swing and trembling trimming are applicable to small or micro-sized products or micro-sized silica gel products rich in metal skeleton, and the rubber edges in the product holes, corners and grooves shall be trimmed together with abrasive.
⑥ Mechanical punching trimming relies on pressure machinery, punching dies and punching knives to remove the rubber edge of the product. This method is applicable to products and model products whose rubber edges can be placed on the bottom plate of a die or punch knife, such as bottle stoppers, leather bowls, etc. For products with high glue content and low hardness, the impact trimming method is usually selected, which can reduce the uneven edge and depression of the side surface formed by the knife cutting due to the large elasticity of the products. However, for products with low glue content and high hardness, the method of knife-edge die can be directly adopted for punching. In addition, punching is also divided into cold cutting and hot cutting. Cold cutting refers to punching under the posture piece at room temperature. The punching pressure of the required equipment is higher and the punching quality is better. Eager means that when punching at a higher temperature, it should be avoided that the time of touching the product at high temperature is too long, thus affecting the product quality.
⑦ Mechanical cutting and trimming is suitable for trimming products with large dimensions, using cutting tools. The cutting machines on one side are all special machines, and different kinds of cutting knives are used for different kinds of products. For example, after the tire is vulcanized, there are rubber strips with divergent lengths on the outer eye and exhaust line. It is necessary to use a grooved device to remove the rubber strips under the condition of tire rotation.
⑧ Mechanical grinding and trimming For mold rubber products with inner holes and outer circles, grinding fances are usually used. The cutting tool for grinding is a grinding wheel with certain thickness of particles. The precision of grinding and trimming is low, and the grinding appearance is rough, which can clamp the remaining sand particles, thus affecting the application effect.
Key words:
Next
Relevant Blog
Methods of bridge reinforcement
2018-08-13
Maintenance and cleaning of rubber molds
2018-08-13
Contact Us
Hotline:
+86-318-8885959
E-mail:
xiaoshoubu@hebeitaile.com
Address:
No.88, Industrial Street, North Industrial Base, Taocheng District, Hengshui City, Hebei Province
Website
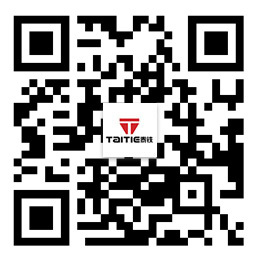
Copyright © Hebei Taile Railway Equipment Co., Ltd