Shrinkage and Quality Problems of Rubber Extruded Semi-finished Products
Release time:
2018-07-13
One. Factors affecting the extrusion process 1. Composition and properties of raw rubber (1) Appropriate selection of raw rubber varieties, in the commonly used rubber varieties, SBR, CR, IIR shrinkage is greater than NR and BR. (2) Add reinforcing filler to reduce the rubber content of raw rubber and reduce the elastic deformation of rubber. The size of carbon black had no effect on the shrinkage of the compound, while the structure and the amount of carbon black had a significant effect on the shrinkage. The higher the structure of carbon black, the greater the amount, the smaller the extrusion shrinkage rate; low reinforcement of anisotropic particles (such as clay, magnesium carbonate, etc.) extrusion shrinkage rate is also small. (3) Adding reclaimed rubber to the rubber compound can increase the flow
1 Factors affecting the extrusion process
1. Composition and properties of raw rubber
(1) appropriate selection of raw rubber varieties, in the commonly used rubber varieties, SBR, CR, IIR shrinkage is greater than NR and BR.
(2) Add reinforcing filler to reduce the rubber content of raw rubber and reduce the elastic deformation of rubber. The size of carbon black had no effect on the shrinkage of the compound, while the structure and the amount of carbon black had a significant effect on the shrinkage. The higher the structure of carbon black, the greater the amount, the smaller the extrusion shrinkage rate; low reinforcement of anisotropic particles (such as clay, magnesium carbonate, etc.) extrusion shrinkage rate is also small.
(3) Adding reclaimed rubber to the rubber compound can increase fluidity and reduce shrinkage.
(4) Adding ointment softener to the rubber compound can play a lubricating role, reduce the shrinkage rate, and make the surface of the product smooth.
(5) rubber plasticity, easy to flow, extrusion shrinkage rate is small.
2. Extrusion temperature
The high extrusion temperature can increase the fluidity of the compound, reduce the expansion rate, and the surface is smooth.
3. Extrusion speed
The greater the extrusion speed, the greater the shrinkage. But the size of the extrusion speed is affected by the following factors:
(1) The larger the mouth cone angle, the higher the smoothness, the faster the extrusion speed, the smoother the surface of the semi-finished product, and the better the compactness.
(2) The plastic degree of the rubber is small and the extrusion speed is slow.
(3) The variety of softeners also has an impact on the extrusion speed. Viscous softeners such as resin and asphalt will slow down the extrusion speed; stearic acid and wax can speed up the extrusion speed.
(4) Different types of reinforcing fillers have different effects on the extrusion speed. The extrusion speed of soft carbon black is faster than that of hard carbon black.
(5) The extrusion temperature increases, which can increase the extrusion speed, but pay attention to the anti-scorch.
4. Cooling of semi-finished products
Uneven cooling, so that the semi-finished products shrinkage deformation is not consistent.
II. Quality Problems and Causes of Extruded Semi-finished Products
The common quality problems in the extrusion process are: the surface of the semi-finished product is not smooth, scorched, bubbles or sponges, uneven thickness, inaccurate specifications and streaks, cracks, etc.
1. The reason why the surface of the semi-finished product is not smooth
Low head and mouth temperature;
The temperature of the glue supply is too high or the temperature of the machine head is too high to cause scorching;
The haulage speed is slow;
Uneven hot blending of rubber material or uneven mixing of return rubber;
Extrusion speed too fast, etc.
2. Main causes of scorching
Improper mixing of rubber material, poor scorch resistance and short scorch time;
The temperature of the machine head is too high; the glue flow port is too small, there is glue accumulation at the machine head or there is a dead angle between the mouth and the machine head, causing the glue to not flow;
Insufficient cooling of the screw; interruption of glue supply, forming empty car stuck glue.
3. Generate bubbles or sponges
Extrusion speed is too fast, so that the air in the compound is not discharged;
The raw material contains more moisture and volatile;
The nose temperature is too high;
Insufficient glue supply.
4. Reasons for uneven thickness
Core type deviation or mouth type is not correct, mouth type plate deformation;
Uneven extrusion temperature control;
The rubber material is unevenly heated, and the extrusion speed is not matched with the traction speed.
5. Reasons for inaccurate specifications
(1) thickness asymmetry, the main reason is the core type deviation or mouth is not right.
(2) The thickness is required, but the width is insufficient or too large, the main reason is that the traction speed is too fast or too slow.
6. Causes of strip cracks
The rubber compound contains impurities or self-sulfur rubber particles;
The plasticity of the rubber material is too small; the extrusion temperature is too high, and the rubber material has a tendency to scorch;
Rough mouth or core;
The glue outlet is blocked;
The pressure of each part is inconsistent.
Key words:
Previous:
Relevant Blog
Methods of bridge reinforcement
2018-08-13
Maintenance and cleaning of rubber molds
2018-08-13
Contact Us
Hotline:
+86-318-8885959
E-mail:
xiaoshoubu@hebeitaile.com
Address:
No.88, Industrial Street, North Industrial Base, Taocheng District, Hengshui City, Hebei Province
Website
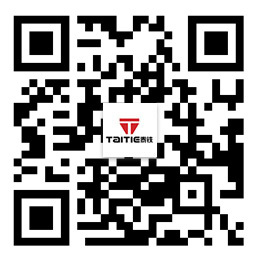
Copyright © Hebei Taile Railway Equipment Co., Ltd